Wyparka przemysłowa to urządzenie, które służy do koncentracji cieczy poprzez odparowanie jej składników lotnych. Proces ten jest niezwykle istotny w wielu branżach, takich jak chemia, farmacja czy spożywcza. Działanie wyparki opiera się na podgrzewaniu cieczy, co powoduje jej odparowanie. W wyniku tego procesu powstaje para wodna, która jest następnie skraplana i usuwana z systemu. Wyparki przemysłowe mogą mieć różne formy i rozmiary, w zależności od potrzeb produkcyjnych danego zakładu. Wyróżniamy między innymi wyparki jednofazowe oraz wielofazowe, które różnią się zarówno konstrukcją, jak i efektywnością działania. Kluczowym elementem wyparki jest wymiennik ciepła, który umożliwia efektywne podgrzewanie cieczy oraz odzyskiwanie energii z pary.
Jakie są zalety stosowania wyparki przemysłowej w produkcji
Stosowanie wyparki przemysłowej w procesach produkcyjnych przynosi wiele korzyści. Przede wszystkim pozwala na znaczną oszczędność czasu i kosztów związanych z obróbką cieczy. Dzięki efektywnemu odparowaniu można uzyskać skoncentrowane produkty w krótszym czasie niż tradycyjne metody. Kolejną zaletą jest możliwość precyzyjnego kontrolowania procesu odparowania, co wpływa na jakość końcowego produktu. Wyparki przemysłowe są również bardzo wszechstronne i mogą być dostosowane do różnych rodzajów cieczy oraz ich właściwości fizykochemicznych. Dodatkowo nowoczesne modele wyparki wyposażone są w systemy automatyzacji, co zwiększa ich efektywność oraz zmniejsza ryzyko błędów ludzkich podczas obsługi.
Jakie są różnice między wyparkami a innymi metodami koncentracji
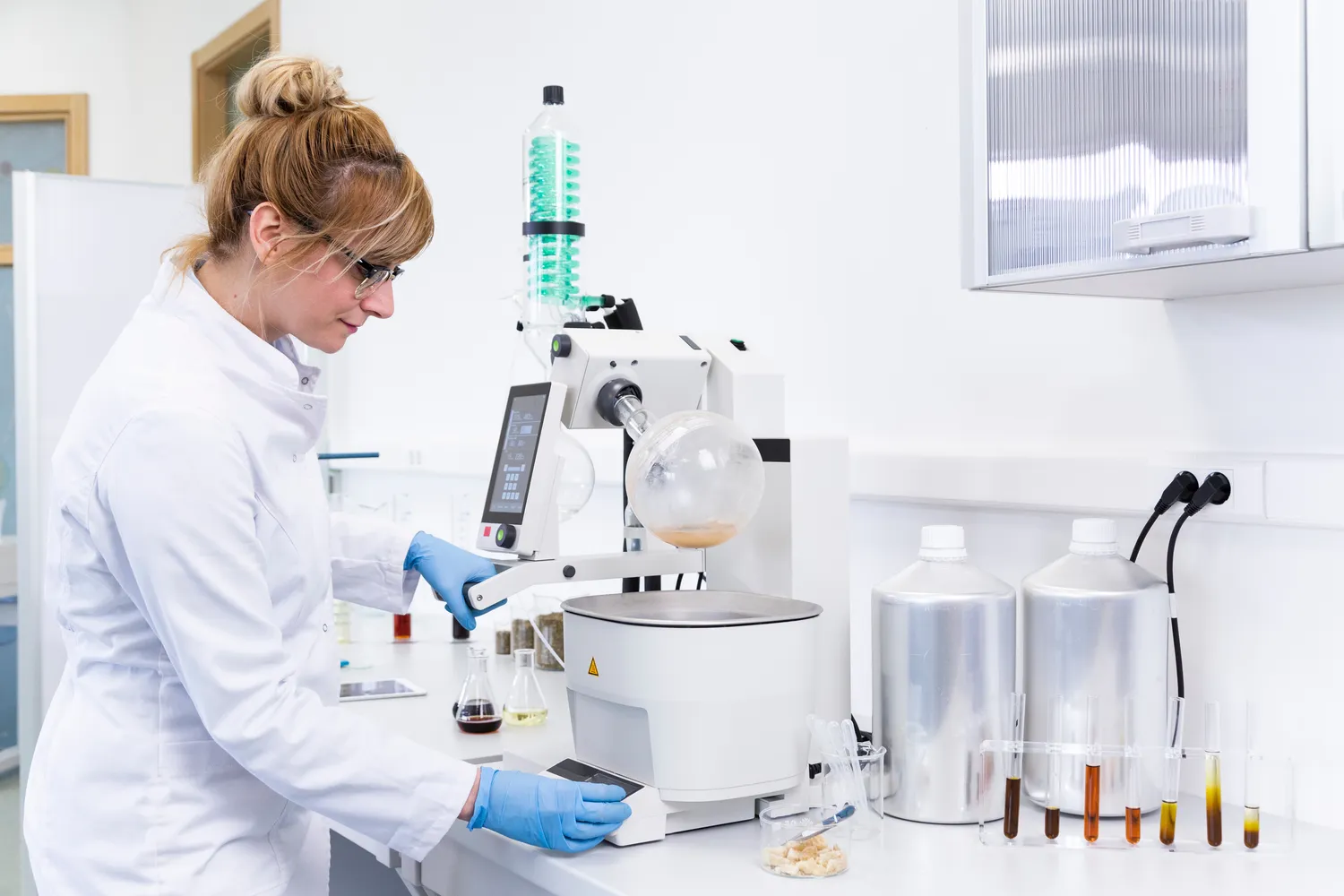
Wyparki przemysłowe wyróżniają się na tle innych metod koncentracji cieczy dzięki swojej efektywności oraz wszechstronności. W porównaniu do tradycyjnych metod takich jak filtracja czy destylacja, wyparki oferują szybsze i bardziej ekonomiczne rozwiązania. Podczas gdy filtracja polega na usuwaniu cząstek stałych z cieczy, a destylacja na oddzielaniu składników na podstawie ich temperatur wrzenia, wyparka koncentruje ciecz poprzez odparowanie nadmiaru wody lub innych składników lotnych. To sprawia, że proces jest znacznie bardziej oszczędny czasowo i energetycznie. Ponadto wyparki mogą być stosowane do szerokiego zakresu substancji, w tym tych o wysokiej lepkości czy dużej zawartości substancji stałych.
Jakie branże korzystają z technologii wyparkowej
Technologia wyparkowa znajduje zastosowanie w wielu branżach przemysłowych, co świadczy o jej uniwersalności i efektywności. Najbardziej powszechnym obszarem wykorzystania są zakłady chemiczne, gdzie procesy koncentracji są kluczowe dla produkcji różnorodnych substancji chemicznych. W branży farmaceutycznej wyparki służą do koncentracji roztworów aktywnych składników leków, co ma istotny wpływ na ich skuteczność oraz stabilność. Również przemysł spożywczy korzysta z technologii wyparkowej do produkcji soków owocowych czy koncentratów smakowych, gdzie istotne jest zachowanie wartości odżywczych i aromatów. Inne branże to m.in. kosmetyczna oraz petrochemiczna, gdzie procesy koncentracji mają kluczowe znaczenie dla jakości produktów końcowych.
Jakie są najczęściej stosowane rodzaje wyparków przemysłowych
Na rynku dostępnych jest wiele różnych rodzajów wyparków przemysłowych, które różnią się konstrukcją, zastosowaniem oraz efektywnością. Jednym z najpopularniejszych typów są wyparki jednokrotnego działania, które przeznaczone są do prostych procesów koncentracji. W tego typu urządzeniach ciecz jest podgrzewana w jednym etapie, a para odprowadzana jest na zewnątrz. Innym rodzajem są wyparki wielokrotnego działania, które umożliwiają wielokrotne wykorzystanie pary wodnej do podgrzewania cieczy. Dzięki temu proces staje się bardziej efektywny energetycznie i ekonomicznie. W branży spożywczej często stosowane są wyparki z wymiennikiem ciepła, które pozwalają na odzyskiwanie energii z pary, co dodatkowo obniża koszty operacyjne. Wyparki próżniowe to kolejny typ, który znajduje zastosowanie w przemyśle farmaceutycznym i chemicznym, gdzie konieczne jest obniżenie temperatury wrzenia cieczy w celu ochrony wrażliwych składników.
Jakie czynniki wpływają na wydajność wyparków przemysłowych
Wydajność wyparków przemysłowych zależy od wielu czynników, które mogą znacząco wpłynąć na efektywność procesu koncentracji. Kluczowym elementem jest temperatura podgrzewania cieczy, która powinna być dostosowana do właściwości fizykochemicznych substancji. Zbyt wysoka temperatura może prowadzić do degradacji składników, podczas gdy zbyt niska może wydłużyć czas procesu. Kolejnym istotnym czynnikiem jest ciśnienie panujące wewnątrz wyparki. W przypadku wyparków próżniowych niższe ciśnienie pozwala na obniżenie temperatury wrzenia cieczy, co jest korzystne dla wrażliwych substancji. Również czas kontaktu cieczy z powierzchnią grzewczą ma znaczenie – im dłużej ciecz pozostaje w kontakcie z gorącą powierzchnią, tym większa jest jej koncentracja. Oprócz tego ważne są także parametry dotyczące przepływu cieczy oraz pary, które powinny być zoptymalizowane w celu osiągnięcia maksymalnej wydajności.
Jakie są koszty eksploatacji wyparków przemysłowych
Koszty eksploatacji wyparków przemysłowych mogą się znacznie różnić w zależności od rodzaju urządzenia oraz specyfiki procesu produkcyjnego. Podstawowe wydatki związane z eksploatacją obejmują koszty energii potrzebnej do podgrzewania cieczy oraz koszty związane z konserwacją i serwisowaniem urządzeń. W przypadku nowoczesnych wyparków wyposażonych w systemy odzysku energii można znacznie obniżyć koszty operacyjne poprzez wykorzystanie ciepła odpadowego do podgrzewania innych procesów produkcyjnych. Dodatkowo warto zwrócić uwagę na koszty związane z surowcami – im bardziej efektywna jest wyparka, tym mniejsze straty materiałowe podczas procesu koncentracji. Koszty pracy również mają znaczenie; automatyzacja procesów pozwala na zmniejszenie liczby pracowników potrzebnych do obsługi urządzeń, co przekłada się na oszczędności finansowe.
Jakie innowacje technologiczne wpływają na rozwój wyparków przemysłowych
Innowacje technologiczne mają kluczowe znaczenie dla rozwoju wyparków przemysłowych i ich efektywności. W ostatnich latach obserwuje się dynamiczny rozwój systemów automatyzacji, które pozwalają na precyzyjne monitorowanie i kontrolowanie parametrów pracy urządzeń. Dzięki zastosowaniu zaawansowanych czujników i systemów informatycznych możliwe jest optymalizowanie procesów w czasie rzeczywistym, co zwiększa wydajność i jakość produktów końcowych. Kolejnym istotnym trendem jest rozwój technologii odzysku energii, która pozwala na minimalizację strat ciepła oraz obniżenie kosztów eksploatacyjnych. Innowacyjne materiały izolacyjne oraz konstrukcje wymienników ciepła przyczyniają się do poprawy efektywności energetycznej wyparków. Również rozwój technologii cyfrowych umożliwia lepsze zarządzanie danymi produkcyjnymi oraz analizę wyników pracy urządzeń, co pozwala na szybsze podejmowanie decyzji dotyczących optymalizacji procesów produkcyjnych.
Jakie są przyszłe kierunki rozwoju technologii wyparkowej
Przyszłość technologii wyparkowej zapowiada się obiecująco dzięki ciągłemu postępowi technologicznemu oraz rosnącemu zapotrzebowaniu na efektywne rozwiązania produkcyjne. Jednym z kluczowych kierunków rozwoju będzie dalsza automatyzacja procesów oraz integracja systemów zarządzania produkcją z technologiami Internetu Rzeczy (IoT). Dzięki temu możliwe będzie zdalne monitorowanie i kontrolowanie pracy wyparków oraz szybsze reagowanie na zmieniające się warunki produkcyjne. Kolejnym istotnym trendem będzie rozwój technologii ekologicznych, które będą miały na celu minimalizację wpływu procesów produkcyjnych na środowisko naturalne. Inwestycje w odnawialne źródła energii oraz technologie odzysku ciepła będą kluczowe dla przyszłości branży. Również rozwój materiałów o lepszych właściwościach termicznych przyczyni się do zwiększenia efektywności energetycznej wyparków przemysłowych.
Jakie są najczęstsze problemy związane z użytkowaniem wyparków
Użytkowanie wyparków przemysłowych wiąże się z pewnymi problemami i wyzwaniami, które mogą wpływać na ich efektywność oraz bezpieczeństwo pracy. Jednym z najczęstszych problemów jest osadzanie się kamienia kotłowego lub innych osadów w wymiennikach ciepła oraz rurach prowadzących ciecz. To może prowadzić do zmniejszenia wydajności wymiany ciepła oraz zwiększonego zużycia energii. Innym istotnym zagadnieniem jest kontrola jakości surowców używanych w procesie – nieodpowiednia jakość może prowadzić do nieprzewidywalnych reakcji chemicznych lub degradacji produktu końcowego. Problemy mogą także wynikać z niewłaściwej kalibracji czujników czy systemu sterowania, co może prowadzić do błędnych ustawień parametrów pracy urządzenia. Zdarza się również awaria elementów mechanicznych lub elektronicznych, co wiąże się z koniecznością przeprowadzenia napraw lub wymiany części.