Destylator przemysłowy to urządzenie, które odgrywa kluczową rolę w wielu procesach produkcyjnych, szczególnie w przemyśle chemicznym i petrochemicznym. Jego głównym zadaniem jest separacja cieczy na podstawie różnic w temperaturze wrzenia składników. Proces ten polega na podgrzewaniu mieszaniny cieczy, co prowadzi do odparowania substancji o niższej temperaturze wrzenia. Para następnie przechodzi przez chłodnicę, gdzie skrapla się z powrotem do postaci cieczy. W ten sposób uzyskuje się produkt o wyższej czystości. W przemyśle destylatory są często wykorzystywane do oczyszczania rozpuszczalników, produkcji alkoholi oraz rafinacji ropy naftowej. Istnieją różne typy destylatorów, takie jak destylatory prostego i frakcyjnego, które różnią się konstrukcją oraz zastosowaniem. Wybór odpowiedniego typu destylatora zależy od specyfiki procesu oraz właściwości surowców, które mają być poddane destylacji.
Jakie są zalety stosowania destylatorów przemysłowych
Stosowanie destylatorów przemysłowych przynosi wiele korzyści dla przedsiębiorstw zajmujących się produkcją chemiczną i pokrewnymi branżami. Przede wszystkim pozwala na uzyskanie wysokiej czystości produktów, co jest kluczowe w przypadku wielu zastosowań przemysłowych. Dzięki precyzyjnemu oddzieleniu składników możliwe jest uzyskanie substancji o pożądanych właściwościach chemicznych i fizycznych. Destylatory przemysłowe są również niezwykle efektywne pod względem energetycznym, co przekłada się na oszczędności kosztów operacyjnych. Dodatkowo nowoczesne technologie umożliwiają automatyzację procesów, co zwiększa wydajność i redukuje ryzyko błędów ludzkich. Warto również wspomnieć o elastyczności tych urządzeń – mogą być dostosowane do różnych rodzajów surowców oraz zmieniających się potrzeb produkcyjnych. Dzięki temu przedsiębiorstwa mogą szybko reagować na zmiany w rynku i dostosowywać swoje procesy do aktualnych wymagań.
Jakie są różne typy destylatorów przemysłowych dostępnych na rynku
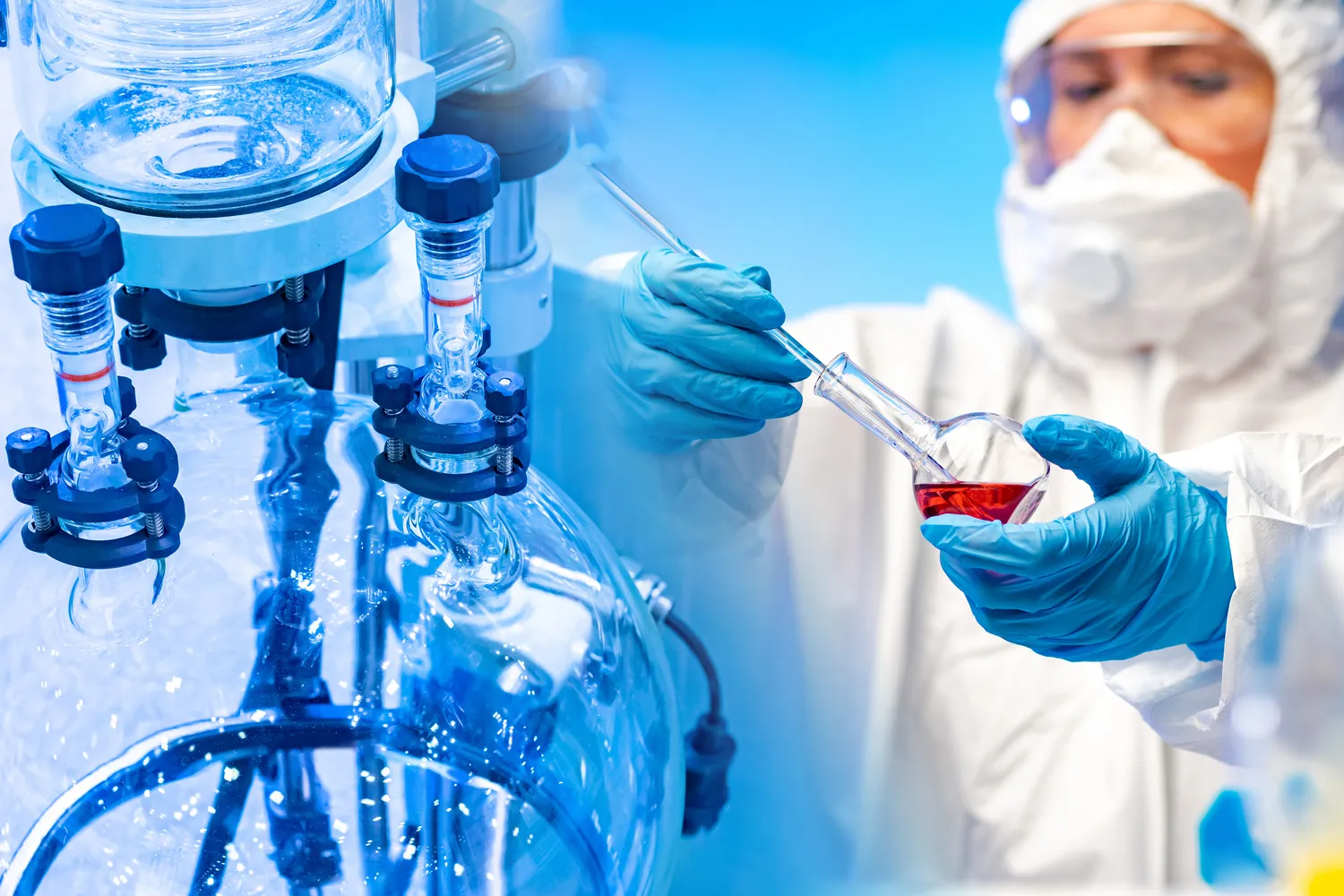
Na rynku dostępnych jest wiele różnych typów destylatorów przemysłowych, które różnią się konstrukcją, zastosowaniem oraz wydajnością. Najpopularniejsze z nich to destylatory proste i frakcyjne. Destylatory proste są najczęściej stosowane do separacji substancji o znacznej różnicy temperatur wrzenia, natomiast destylatory frakcyjne pozwalają na bardziej skomplikowane procesy separacji, gdzie składniki mają zbliżone temperatury wrzenia. W przypadku dużych zakładów przemysłowych często wykorzystuje się kolumny destylacyjne, które charakteryzują się dużą powierzchnią kontaktu między parą a cieczą, co zwiększa efektywność procesu. Innym rodzajem są destylatory próżniowe, które umożliwiają przeprowadzanie procesów w obniżonym ciśnieniu, co pozwala na destylację substancji w niższych temperaturach i minimalizuje ryzyko ich degradacji. W ostatnich latach coraz większą popularnością cieszą się także destylatory membranowe oraz te wykorzystujące technologię osmozy odwrotnej.
Jakie są zastosowania destylatorów przemysłowych w różnych branżach
Destylatory przemysłowe znajdują szerokie zastosowanie w różnych branżach gospodarki, co czyni je niezwykle wszechstronnymi urządzeniami. W przemyśle chemicznym są kluczowym elementem procesów produkcyjnych związanych z syntezą chemiczną oraz oczyszczaniem substancji chemicznych. Na przykład w produkcji alkoholu etylowego destylatory służą do oddzielania etanolu od innych składników fermentacyjnych, co pozwala uzyskać wysokiej jakości napój alkoholowy. W branży petrochemicznej destylacja jest niezbędna do rafinacji ropy naftowej – dzięki niej możliwe jest uzyskanie różnych frakcji paliwowych oraz surowców chemicznych. Ponadto w przemyśle farmaceutycznym destylatory są wykorzystywane do oczyszczania rozpuszczalników oraz produkcji substancji czynnych leków. Również w sektorze spożywczym znajdują zastosowanie przy produkcji olejków eterycznych czy ekstraktów smakowych.
Jakie są kluczowe czynniki wpływające na efektywność destylacji przemysłowej
Efektywność procesu destylacji przemysłowej zależy od wielu czynników, które mogą znacząco wpłynąć na jakość uzyskiwanych produktów oraz koszty operacyjne. Jednym z najważniejszych aspektów jest temperatura, która musi być precyzyjnie kontrolowana, aby zapewnić optymalne warunki do odparowania i skraplania składników. Zbyt wysoka temperatura może prowadzić do degradacji niektórych substancji, podczas gdy zbyt niska może skutkować niepełną separacją. Kolejnym kluczowym czynnikiem jest ciśnienie, które ma bezpośredni wpływ na temperatury wrzenia cieczy. W przypadku destylacji próżniowej, obniżone ciśnienie pozwala na przeprowadzanie procesów w niższych temperaturach, co jest korzystne dla wrażliwych chemikaliów. Ważnym elementem jest także konstrukcja samego destylatora, w tym rodzaj kolumny oraz materiały użyte do budowy. Odpowiednio dobrane materiały mogą zwiększyć odporność na korozję i wydłużyć żywotność urządzenia. Dodatkowo, zastosowanie odpowiednich katalizatorów oraz technik mieszania może przyczynić się do poprawy efektywności procesu.
Jakie są najnowsze technologie w dziedzinie destylacji przemysłowej
W ostatnich latach w dziedzinie destylacji przemysłowej nastąpił znaczny postęp technologiczny, który przyczynił się do zwiększenia efektywności i bezpieczeństwa procesów. Nowoczesne destylatory często wykorzystują zaawansowane systemy automatyzacji, które pozwalają na zdalne monitorowanie i sterowanie procesami produkcyjnymi. Dzięki temu operatorzy mogą szybko reagować na zmiany warunków pracy oraz minimalizować ryzyko awarii. Wprowadzenie technologii cyfrowych umożliwia także zbieranie danych o wydajności urządzeń, co pozwala na ich optymalizację i przewidywanie potrzeb serwisowych. Kolejnym innowacyjnym rozwiązaniem są destylatory membranowe, które wykorzystują różnice w przepuszczalności membran do separacji składników. Ta metoda charakteryzuje się mniejszym zużyciem energii oraz większą selektywnością niż tradycyjne metody destylacji. Ponadto rozwijają się technologie związane z wykorzystaniem energii odnawialnej w procesach destylacyjnych, co wpisuje się w globalne trendy zrównoważonego rozwoju. Przykładem mogą być systemy wykorzystujące energię słoneczną do podgrzewania cieczy przed procesem destylacji.
Jakie są wyzwania związane z eksploatacją destylatorów przemysłowych
Eksploatacja destylatorów przemysłowych wiąże się z wieloma wyzwaniami, które mogą wpływać na ich wydajność oraz bezpieczeństwo pracy. Jednym z głównych problemów jest korozja materiałów użytych do budowy urządzeń, szczególnie w przypadku przetwarzania agresywnych chemikaliów. Właściwy dobór materiałów oraz regularna konserwacja są kluczowe dla zapewnienia długotrwałej eksploatacji destylatorów. Innym istotnym wyzwaniem jest zarządzanie odpadami powstającymi w wyniku procesów destylacyjnych. Wiele substancji chemicznych może być szkodliwych dla środowiska, dlatego konieczne jest wdrożenie odpowiednich procedur ich utylizacji lub recyklingu. Dodatkowo operatorzy muszą zmagać się z problemami związanymi z utrzymaniem stabilności procesu, co może być trudne w przypadku zmiennych warunków surowcowych czy sezonowych fluktuacji popytu. W kontekście bezpieczeństwa pracy istotne jest również przestrzeganie norm i regulacji dotyczących obsługi urządzeń oraz ochrony zdrowia pracowników.
Jakie są przyszłe kierunki rozwoju technologii destylacyjnych
Przyszłość technologii destylacyjnych zapowiada się obiecująco dzięki ciągłemu rozwojowi innowacyjnych rozwiązań oraz rosnącemu zainteresowaniu zrównoważonym rozwojem w przemyśle. Jednym z kluczowych kierunków rozwoju będzie dalsza automatyzacja procesów produkcyjnych, co pozwoli na zwiększenie efektywności oraz redukcję kosztów operacyjnych. Systemy sztucznej inteligencji i uczenia maszynowego będą mogły analizować dane dotyczące wydajności urządzeń i sugerować optymalne parametry pracy, co przyczyni się do poprawy jakości produktów końcowych. Również rozwój technologii związanych z odzyskiem ciepła i energii będzie miał istotny wpływ na przyszłość destylacji przemysłowej – zastosowanie systemów kogeneracyjnych czy pompy ciepła może znacznie obniżyć zużycie energii w procesach produkcyjnych. Ponadto coraz większe znaczenie będą miały technologie związane z recyklingiem i ponownym wykorzystaniem surowców wtórnych, co wpisuje się w globalne trendy proekologiczne i odpowiedzialnego zarządzania zasobami naturalnymi.
Jakie są przykłady zastosowania destylatorów przemysłowych w praktyce
Przykłady zastosowania destylatorów przemysłowych można znaleźć w wielu branżach, ilustrując ich wszechstronność oraz znaczenie dla współczesnej gospodarki. W przemyśle alkoholowym destylatory są wykorzystywane do produkcji różnych rodzajów napojów spirytusowych, takich jak whisky czy gin. Proces ten polega na wielokrotnej distylacji surowców fermentacyjnych, co pozwala uzyskać wysokiej jakości produkt o pożądanym smaku i aromacie. W branży petrochemicznej rafinacja ropy naftowej to kolejny przykład zastosowania tych urządzeń – dzięki nim możliwe jest oddzielanie różnych frakcji paliwowych oraz surowców chemicznych wykorzystywanych w produkcji plastiku czy detergentów. Destylatory znajdują również zastosowanie w przemyśle farmaceutycznym, gdzie służą do oczyszczania substancji czynnych leków oraz rozpuszczalników wykorzystywanych w procesach produkcyjnych. Inny przykład to produkcja olejków eterycznych z roślin – poprzez destylację parową uzyskuje się cenne ekstrakty stosowane w kosmetykach czy aromaterapii.