Destylarka do rozpuszczalników to urządzenie, które wykorzystuje proces destylacji w celu oddzielenia różnych substancji chemicznych na podstawie ich temperatury wrzenia. W praktyce oznacza to, że rozpuszczalniki o niższej temperaturze wrzenia są odparowywane i skraplane, co pozwala na ich zbieranie w czystej postaci. Tego rodzaju urządzenia znajdują zastosowanie w wielu dziedzinach, takich jak przemysł chemiczny, farmaceutyczny czy kosmetyczny. Dzięki nim możliwe jest uzyskanie wysokiej czystości substancji, co jest kluczowe dla wielu procesów produkcyjnych. W przypadku destylacji rozpuszczalników istotne jest również zapewnienie odpowiednich warunków pracy, takich jak kontrola temperatury oraz ciśnienia, co wpływa na efektywność procesu. Warto zaznaczyć, że destylarki mogą mieć różne konstrukcje i pojemności, co sprawia, że są dostosowane do różnych potrzeb użytkowników.
Jakie rodzaje destylarek do rozpuszczalników są dostępne na rynku
Na rynku dostępnych jest wiele różnych rodzajów destylarek do rozpuszczalników, które różnią się zarówno budową, jak i przeznaczeniem. Jednym z najpopularniejszych typów są destylarki laboratoryjne, które charakteryzują się niewielkimi rozmiarami oraz precyzyjnym działaniem. Są one idealne do użytku w laboratoriach chemicznych oraz badawczych, gdzie wymagana jest wysoka jakość uzyskiwanych substancji. Innym rodzajem są destylarki przemysłowe, które mają większą pojemność i są przystosowane do ciągłej pracy w warunkach przemysłowych. Takie urządzenia często wyposażone są w automatyczne systemy sterowania oraz monitorowania procesu destylacji, co zwiększa ich efektywność. Warto również wspomnieć o mobilnych destylarkach, które można łatwo transportować i wykorzystywać w różnych lokalizacjach. Te urządzenia znajdują zastosowanie w sytuacjach awaryjnych lub tam, gdzie nie ma dostępu do stałych instalacji.
Jakie materiały są używane w budowie destylarek do rozpuszczalników
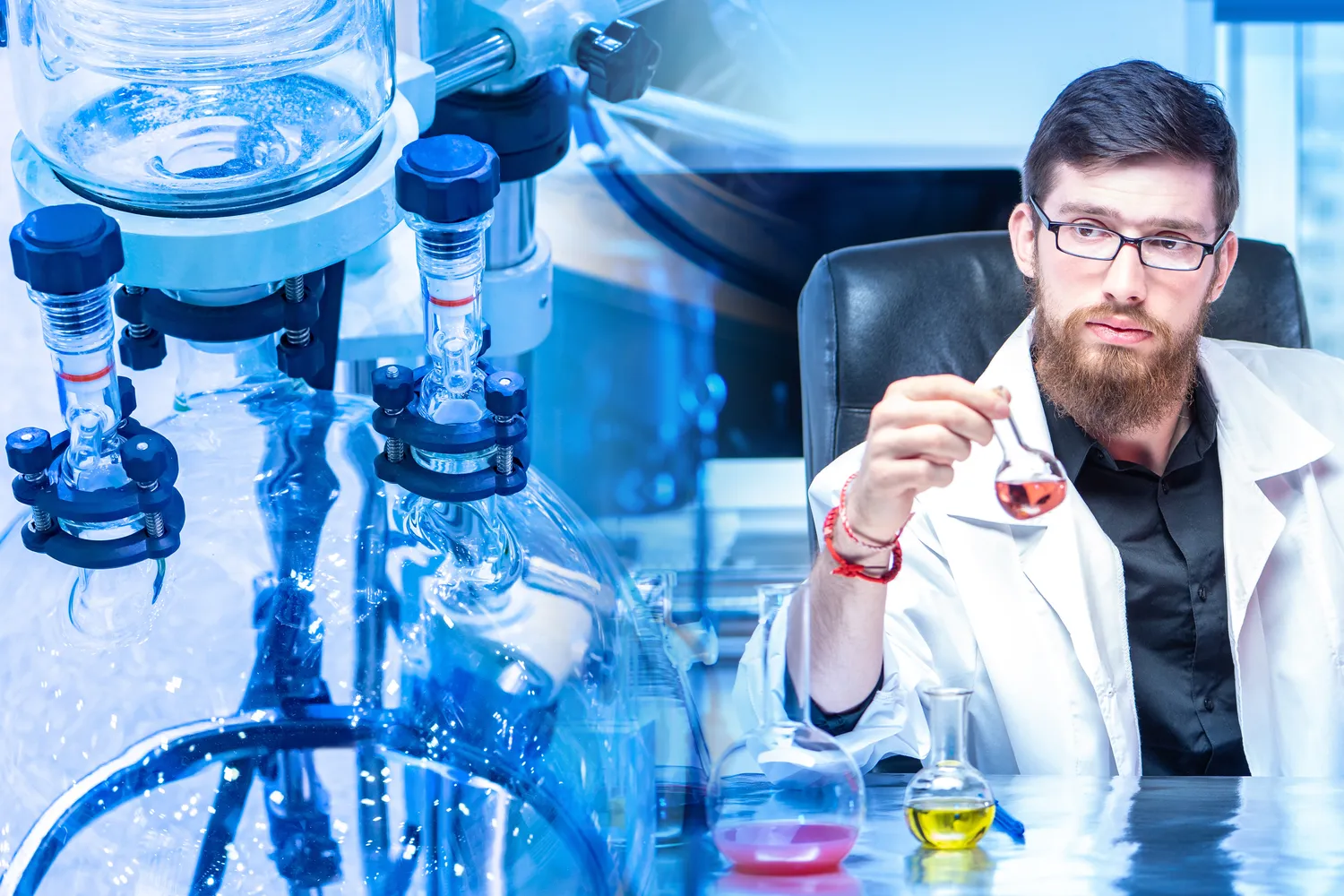
Budowa destylarek do rozpuszczalników opiera się na zastosowaniu materiałów odpornych na działanie chemikaliów oraz wysokich temperatur. Najczęściej wykorzystywanym materiałem jest stal nierdzewna, która charakteryzuje się dużą odpornością na korozję oraz trwałością. Stal nierdzewna jest idealna do kontaktu z różnymi substancjami chemicznymi i zapewnia długotrwałe użytkowanie urządzenia bez obaw o jego uszkodzenie. W niektórych przypadkach stosuje się także szkło borokrzemowe, które jest odporne na wysokie temperatury oraz działanie agresywnych substancji chemicznych. Szkło jest szczególnie popularne w laboratoriach ze względu na swoją przezroczystość, co umożliwia łatwe monitorowanie procesu destylacji. Dodatkowo elementy takie jak uszczelki czy zawory często wykonane są z materiałów odpornych na działanie chemikaliów, aby zapewnić szczelność całego systemu. W przypadku bardziej zaawansowanych modeli można spotkać także elementy wykonane z teflonu lub innych tworzyw sztucznych odpornych na wysokie temperatury i działanie substancji chemicznych.
Jakie są zalety korzystania z destylarki do rozpuszczalników
Korzystanie z destylarki do rozpuszczalników niesie ze sobą wiele korzyści zarówno dla użytkowników indywidualnych, jak i dla przemysłu. Przede wszystkim umożliwia ona uzyskanie wysokiej czystości substancji chemicznych poprzez skuteczne oddzielanie ich od zanieczyszczeń oraz innych składników. Dzięki temu możliwe jest prowadzenie precyzyjnych badań laboratoryjnych oraz produkcja wysokiej jakości produktów w przemyśle chemicznym czy farmaceutycznym. Kolejną zaletą jest oszczędność kosztów związana z możliwością ponownego wykorzystania rozpuszczalników po ich oczyszczeniu. Destylacja pozwala na odzyskiwanie cennych substancji chemicznych, co może znacząco obniżyć koszty produkcji oraz zmniejszyć ilość odpadów chemicznych generowanych podczas procesów przemysłowych. Dodatkowo nowoczesne destylarki często wyposażone są w zaawansowane systemy monitorowania oraz automatyzacji procesów, co zwiększa komfort pracy i minimalizuje ryzyko błędów ludzkich.
Jakie są najczęstsze zastosowania destylarek do rozpuszczalników w przemyśle
Destylarki do rozpuszczalników znajdują szerokie zastosowanie w różnych gałęziach przemysłu, co czyni je niezwykle wszechstronnymi urządzeniami. W przemyśle chemicznym są one wykorzystywane do oczyszczania i separacji rozpuszczalników organicznych, które są niezbędne w wielu procesach produkcyjnych. Dzięki destylacji możliwe jest uzyskanie czystych substancji, które mogą być następnie stosowane jako surowce do produkcji innych chemikaliów. W branży farmaceutycznej destylarki odgrywają kluczową rolę w procesie produkcji leków, gdzie wysoka jakość i czystość składników aktywnych są niezbędne dla bezpieczeństwa pacjentów. W kosmetykach również wykorzystuje się destylację do uzyskiwania czystych olejków eterycznych oraz innych substancji czynnych, które mają korzystny wpływ na skórę. Oprócz tego, destylarki znajdują zastosowanie w przemyśle spożywczym, gdzie służą do ekstrakcji aromatów oraz konserwantów z naturalnych surowców.
Jakie są kluczowe czynniki przy wyborze destylarki do rozpuszczalników
Wybór odpowiedniej destylarki do rozpuszczalników jest kluczowy dla efektywności i bezpieczeństwa pracy. Przede wszystkim należy zwrócić uwagę na pojemność urządzenia, która powinna być dostosowana do potrzeb użytkownika. Dla małych laboratoriów wystarczające będą mniejsze modele, podczas gdy w przemyśle mogą być potrzebne większe urządzenia zdolne do ciągłej pracy. Kolejnym istotnym czynnikiem jest materiał, z którego wykonana jest destylarka. Stal nierdzewna oraz szkło borokrzemowe to najczęściej wybierane materiały ze względu na swoją odporność na działanie chemikaliów i wysokich temperatur. Ważne jest także wyposażenie destylarki w systemy automatyzacji oraz monitorowania procesu, co pozwala na łatwiejszą obsługę i zwiększa bezpieczeństwo pracy. Użytkownicy powinni również zwrócić uwagę na dostępność części zamiennych oraz serwisu posprzedażowego oferowanego przez producenta, co może mieć znaczenie w przypadku awarii lub konieczności przeprowadzenia konserwacji.
Jakie są najnowsze trendy w technologii destylacji rozpuszczalników
W ostatnich latach technologia destylacji rozpuszczalników uległa znacznym zmianom dzięki postępom w dziedzinie inżynierii chemicznej oraz automatyzacji procesów przemysłowych. Jednym z najważniejszych trendów jest rozwój inteligentnych systemów sterowania, które umożliwiają monitorowanie i optymalizację procesów destylacji w czasie rzeczywistym. Dzięki zastosowaniu zaawansowanych algorytmów oraz czujników możliwe jest dostosowywanie parametrów pracy urządzenia do zmieniających się warunków, co przekłada się na zwiększenie efektywności oraz oszczędność energii. Innowacyjne rozwiązania obejmują także wykorzystanie technologii membranowej oraz ekstrakcji cieczy nadkrytycznej jako alternatywy dla tradycyjnej destylacji, co pozwala na uzyskiwanie wyższej czystości produktów końcowych. Warto również zauważyć rosnące zainteresowanie ekologicznymi metodami oczyszczania rozpuszczalników, które minimalizują negatywny wpływ na środowisko naturalne. Producenci coraz częściej inwestują w technologie pozwalające na recykling rozpuszczalników oraz redukcję odpadów chemicznych generowanych podczas procesów produkcyjnych.
Jakie są najczęstsze problemy związane z użytkowaniem destylarek do rozpuszczalników
Mimo że destylarki do rozpuszczalników są niezwykle przydatnymi urządzeniami, ich użytkowanie może wiązać się z pewnymi problemami. Jednym z najczęstszych wyzwań jest zapewnienie odpowiednich warunków pracy, takich jak kontrola temperatury i ciśnienia. Niewłaściwe ustawienia mogą prowadzić do nieefektywnej destylacji lub nawet uszkodzenia sprzętu. Kolejnym problemem może być zanieczyszczenie rozpuszczalników, które wpływa na jakość uzyskiwanych produktów końcowych. Dlatego ważne jest regularne monitorowanie stanu używanych substancji oraz przeprowadzanie odpowiednich analiz chemicznych przed rozpoczęciem procesu destylacji. Użytkownicy powinni także dbać o konserwację urządzeń, aby uniknąć awarii związanych z zużyciem elementów czy osadzaniem się zanieczyszczeń wewnątrz systemu. Często występującym problemem jest również niewłaściwe użytkowanie sprzętu przez personel, co może prowadzić do niebezpiecznych sytuacji lub obniżenia efektywności pracy.
Jakie przepisy prawne regulują użytkowanie destylarek do rozpuszczalników
Użytkowanie destylarek do rozpuszczalników podlega różnorodnym regulacjom prawnym, które mają na celu zapewnienie bezpieczeństwa zarówno pracowników, jak i ochrony środowiska naturalnego. W wielu krajach istnieją przepisy dotyczące klasyfikacji substancji chemicznych oraz ich transportu, które muszą być przestrzegane przez użytkowników tych urządzeń. W Unii Europejskiej obowiązuje system REACH (Registration, Evaluation, Authorisation and Restriction of Chemicals), który reguluje stosowanie substancji chemicznych oraz wymaga rejestracji nowych substancji przed ich wprowadzeniem na rynek. Ponadto przepisy BHP nakładają obowiązki dotyczące szkolenia pracowników oraz zapewnienia odpowiednich środków ochrony osobistej podczas pracy z substancjami chemicznymi i urządzeniami takimi jak destylarki. Użytkownicy muszą także przestrzegać norm dotyczących emisji zanieczyszczeń oraz zarządzania odpadami chemicznymi generowanymi podczas procesów produkcyjnych.
Jakie są koszty zakupu i eksploatacji destylarki do rozpuszczalników
Koszty zakupu i eksploatacji destylarki do rozpuszczalników mogą znacznie się różnić w zależności od modelu, pojemności oraz dodatkowych funkcji oferowanych przez producenta. Przy zakupie należy uwzględnić nie tylko cenę samego urządzenia, ale także koszty związane z jego instalacją oraz ewentualnymi modyfikacjami infrastruktury laboratoryjnej lub przemysłowej. Koszt zakupu podstawowej destylarki laboratoryjnej może wynosić od kilku tysięcy złotych do kilkudziesięciu tysięcy złotych za bardziej zaawansowane modele przemysłowe. Poza kosztami początkowymi istotne są także wydatki związane z eksploatacją urządzenia, takie jak zużycie energii elektrycznej czy koszty konserwacji i serwisowania sprzętu. Regularna konserwacja jest kluczowa dla utrzymania wysokiej wydajności i bezpieczeństwa pracy urządzenia, co wiąże się z dodatkowymi kosztami serwisowymi.