Destylacja rozpuszczalników to proces, który ma na celu oddzielenie składników mieszaniny na podstawie różnicy ich temperatur wrzenia. W praktyce oznacza to, że kiedy mieszanina jest podgrzewana, składnik o niższej temperaturze wrzenia paruje jako pierwszy, a następnie skrapla się w chłodniejszej części aparatury destylacyjnej. Kluczowym elementem tego procesu jest użycie odpowiednich urządzeń, takich jak kolumna destylacyjna czy kondensator. W zależności od rodzaju rozpuszczalników i ich właściwości fizycznych, proces destylacji może być przeprowadzany w różnych warunkach ciśnienia i temperatury. Ważne jest również, aby zrozumieć, że nie wszystkie rozpuszczalniki można oddzielić za pomocą standardowej destylacji; czasami konieczne jest zastosowanie bardziej zaawansowanych technik, takich jak destylacja frakcyjna lub destylacja pod ciśnieniem. Warto również zwrócić uwagę na czystość używanych rozpuszczalników oraz na ich potencjalne zanieczyszczenia, które mogą wpływać na efektywność procesu.
Jakie są zastosowania destylacji rozpuszczalników w przemyśle
Destylacja rozpuszczalników znajduje szerokie zastosowanie w różnych gałęziach przemysłu, co czyni ją niezwykle istotnym procesem technologicznym. W przemyśle chemicznym jest wykorzystywana do oczyszczania surowców oraz produktów końcowych, co pozwala na uzyskanie wysokiej jakości substancji chemicznych. Na przykład w produkcji alkoholi etylowych destylacja jest kluczowym etapem, który umożliwia oddzielenie etanolu od innych składników fermentacji. W przemyśle petrochemicznym proces ten jest stosowany do separacji różnych frakcji ropy naftowej, co pozwala na uzyskanie paliw oraz innych produktów chemicznych o określonych właściwościach. Również w farmaceutyce destylacja odgrywa ważną rolę w produkcji leków oraz substancji czynnych, gdzie czystość i jakość są kluczowe dla bezpieczeństwa pacjentów. Ponadto, w laboratoriach chemicznych destylacja jest często stosowana do przygotowywania prób do dalszych badań analitycznych.
Jakie są różnice między destylacją a innymi metodami separacji
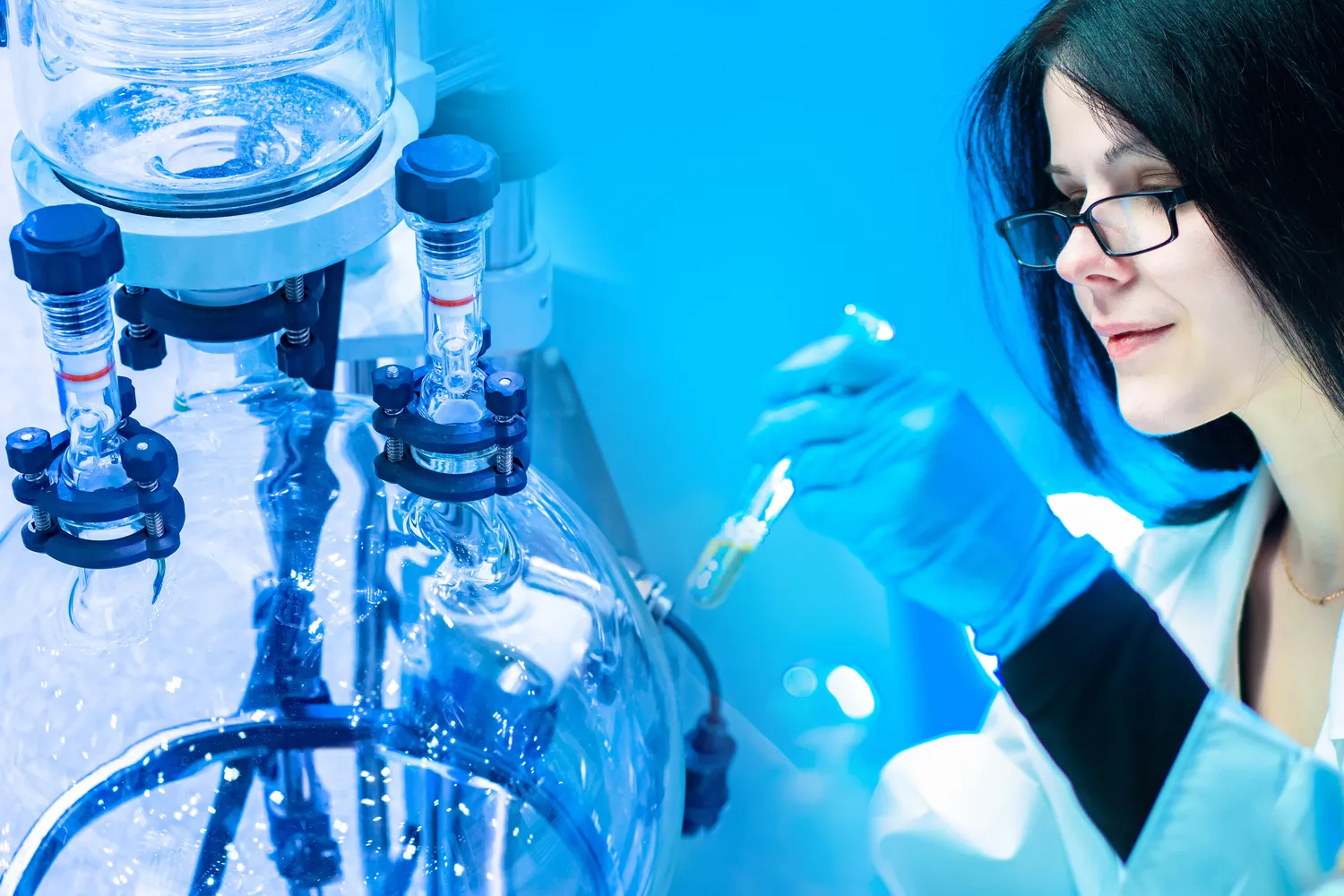
W kontekście separacji składników mieszanin chemicznych istnieje wiele metod obok destylacji, które różnią się zasadą działania oraz zastosowaniem. Destylacja opiera się głównie na różnicy temperatur wrzenia składników, co sprawia, że jest szczególnie skuteczna w przypadku cieczy. Z kolei inne metody separacji, takie jak ekstrakcja czy chromatografia, wykorzystują różnice w rozpuszczalności lub adsorpcji substancji na różnych nośnikach. Ekstrakcja polega na przenoszeniu jednego lub więcej składników z jednej fazy do drugiej i często jest stosowana w przypadkach, gdy składniki mają podobne temperatury wrzenia. Chromatografia natomiast to technika separacyjna oparta na różnicach w szybkości migracji składników przez materiał adsorbujący i jest niezwykle przydatna w analizach chemicznych oraz biochemicznych. Warto zauważyć, że wybór metody separacji zależy od specyfiki danej mieszaniny oraz pożądanej czystości końcowego produktu.
Jakie są najczęstsze błędy podczas destylacji rozpuszczalników
Podczas przeprowadzania procesu destylacji rozpuszczalników mogą wystąpić liczne błędy, które mogą znacząco wpłynąć na efektywność oraz jakość uzyskanego produktu. Jednym z najczęstszych problemów jest niewłaściwe ustawienie temperatury grzania; zbyt wysoka temperatura może prowadzić do niekontrolowanego parowania i utraty cennych składników. Z kolei zbyt niska temperatura może skutkować niepełnym oddzieleniem substancji. Kolejnym istotnym błędem jest niewłaściwe dobranie aparatury destylacyjnej; użycie kolumny o niewłaściwej wysokości lub średnicy może prowadzić do nieefektywnego procesu separacji. Ważne jest również monitorowanie ciśnienia wewnątrz systemu; zmiany ciśnienia mogą wpływać na temperatury wrzenia składników i tym samym na efektywność procesu. Nie można zapominać o czystości używanych materiałów; zanieczyszczenia mogą wpłynąć na wyniki analizy oraz jakość końcowego produktu.
Jakie są nowoczesne technologie w destylacji rozpuszczalników
W ostatnich latach nastąpił znaczący rozwój technologii związanych z destylacją rozpuszczalników, co pozwala na zwiększenie efektywności i redukcję kosztów operacyjnych. Nowoczesne systemy destylacyjne często wykorzystują automatyzację oraz zaawansowane oprogramowanie do monitorowania i kontrolowania parametrów procesu. Dzięki temu możliwe jest precyzyjne dostosowanie temperatury, ciśnienia oraz innych istotnych czynników, co przekłada się na lepszą jakość uzyskiwanych produktów. Warto również zwrócić uwagę na zastosowanie technologii membranowych, które mogą być stosowane jako uzupełnienie tradycyjnej destylacji. Membrany umożliwiają selektywne oddzielanie składników na podstawie ich wielkości lub ładunku, co może prowadzić do oszczędności energii oraz zmniejszenia ilości odpadów. Kolejnym innowacyjnym podejściem jest wykorzystanie destylacji azeotropowej, która pozwala na separację składników w przypadku mieszanin tworzących azeotropy, co jest szczególnie trudne w tradycyjnych procesach destylacyjnych. Wprowadzenie nowych materiałów konstrukcyjnych do budowy kolumn destylacyjnych oraz kondensatorów również przyczynia się do poprawy efektywności energetycznej i wydajności całego procesu.
Jakie są różnice między destylacją frakcyjną a prostą
Destylacja frakcyjna i prosta to dwie podstawowe metody separacji składników mieszanin cieczy, które różnią się zarówno zasadą działania, jak i zastosowaniem. Destylacja prosta jest najczęściej stosowana w przypadku mieszanin składających się z dwóch składników o znacznie różniących się temperaturach wrzenia. Proces ten polega na podgrzewaniu mieszaniny do momentu, gdy jeden ze składników zaczyna parować, a następnie skraplaniu pary w chłodniejszej części aparatury. Jest to metoda stosunkowo szybka i łatwa do przeprowadzenia, jednak jej skuteczność maleje w przypadku bardziej złożonych mieszanin. Z kolei destylacja frakcyjna jest bardziej zaawansowaną techniką, która pozwala na separację wielu składników o zbliżonych temperaturach wrzenia. W tym przypadku stosuje się kolumnę destylacyjną, która umożliwia wielokrotne parowanie i skraplanie składników, co prowadzi do ich lepszego rozdzielenia. Dzięki temu destylacja frakcyjna jest szczególnie przydatna w przemyśle chemicznym oraz petrochemicznym, gdzie często zachodzi potrzeba oddzielenia wielu frakcji ropy naftowej czy różnych alkoholi.
Jakie są wyzwania związane z bezpieczeństwem podczas destylacji rozpuszczalników
Bezpieczeństwo podczas procesu destylacji rozpuszczalników jest kluczowym aspektem, który nie powinien być bagatelizowany. Wiele rozpuszczalników jest substancjami łatwopalnymi lub toksycznymi, co stwarza ryzyko pożaru lub zatrucia dla pracowników oraz środowiska. Dlatego niezwykle ważne jest przestrzeganie odpowiednich norm i procedur bezpieczeństwa podczas przeprowadzania tego typu procesów. Przede wszystkim należy zapewnić odpowiednią wentylację w pomieszczeniu, w którym odbywa się destylacja; to pomoże zminimalizować ryzyko gromadzenia się szkodliwych oparów. Użycie odpowiedniej aparatury oraz materiałów odpornych na działanie wysokich temperatur i chemikaliów również ma kluczowe znaczenie dla bezpieczeństwa procesu. Regularne kontrole sprzętu oraz szkolenia dla pracowników są niezbędne, aby zapewnić prawidłowe funkcjonowanie systemu oraz minimalizować ryzyko awarii. Ponadto warto inwestować w nowoczesne technologie monitorujące, które mogą wykrywać niebezpieczne sytuacje i automatycznie reagować na zagrożenia.
Jakie są korzyści ekonomiczne wynikające z efektywnej destylacji
Efektywna destylacja rozpuszczalników niesie ze sobą wiele korzyści ekonomicznych dla przedsiębiorstw zajmujących się produkcją chemiczną czy farmaceutyczną. Przede wszystkim poprawa jakości uzyskiwanych produktów przekłada się na większe zyski; czystsze substancje są bardziej pożądane na rynku i mogą być sprzedawane po wyższych cenach. Ponadto optymalizacja procesu destylacji pozwala na zmniejszenie zużycia energii oraz surowców, co bezpośrednio wpływa na obniżenie kosztów operacyjnych. Wdrożenie nowoczesnych technologii oraz automatyzacja procesów mogą również przyczynić się do zwiększenia wydajności produkcji; mniej czasu spędzonego na przetwarzaniu oznacza większą ilość wyprodukowanych substancji w krótszym czasie. Dodatkowo efektywna destylacja może prowadzić do redukcji odpadów oraz emisji szkodliwych substancji do środowiska, co jest coraz bardziej istotnym czynnikiem w kontekście regulacji prawnych oraz wymagań społecznych dotyczących ochrony środowiska.
Jakie są przyszłe kierunki rozwoju technologii destylacji
Przyszłość technologii destylacji rozpuszczalników zapowiada się obiecująco dzięki ciągłemu postępowi naukowemu oraz technologicznemu. Jednym z głównych kierunków rozwoju jest poszukiwanie bardziej ekologicznych metod separacji składników, które minimalizują zużycie energii oraz ograniczają negatywny wpływ na środowisko naturalne. Techniki takie jak zielona chemia czy biotechnologia mogą odegrać kluczową rolę w opracowywaniu nowych procesów destylacyjnych opartych na odnawialnych surowcach i mniej szkodliwych chemikaliach. Również rozwój nanotechnologii otwiera nowe możliwości w zakresie materiałów wykorzystywanych w aparaturze destylacyjnej; nanomateriały mogą poprawić efektywność procesów separacyjnych poprzez zwiększenie powierzchni kontaktu między fazami czy poprawę przewodnictwa cieplnego. Automatyzacja i sztuczna inteligencja również będą miały coraz większe znaczenie; inteligentne systemy monitorujące mogą dostarczać danych w czasie rzeczywistym i optymalizować parametry procesu w celu maksymalizacji wydajności i jakości produktów.