Budowa maszyn pneumatycznych opiera się na kilku kluczowych elementach, które współpracują ze sobą, aby zapewnić efektywne działanie systemu. Na początku warto zwrócić uwagę na sprężarki powietrza, które są sercem każdego systemu pneumatycznego. Ich zadaniem jest sprężanie powietrza do odpowiedniego ciśnienia, co umożliwia jego późniejsze wykorzystanie w różnych aplikacjach. Kolejnym istotnym elementem są zbiorniki powietrza, które gromadzą sprężone powietrze i utrzymują je pod stałym ciśnieniem. Zbiorniki te muszą być odpowiednio zaprojektowane, aby wytrzymać wysokie ciśnienia i nie ulegać uszkodzeniom. Następnie mamy do czynienia z różnymi rodzajami zaworów, które kontrolują przepływ powietrza w systemie. Zawory te mogą być ręczne lub automatyczne i odgrywają kluczową rolę w zarządzaniu pracą maszyny. Oprócz tego nie można zapomnieć o siłownikach pneumatycznych, które przekształcają energię sprężonego powietrza w ruch mechaniczny. Siłowniki te są dostępne w różnych kształtach i rozmiarach, co pozwala na ich zastosowanie w wielu różnych aplikacjach przemysłowych.
Jakie są zalety i wady maszyn pneumatycznych
Maszyny pneumatyczne mają wiele zalet, które przyciągają uwagę inżynierów i przedsiębiorców w różnych branżach. Przede wszystkim ich główną zaletą jest prostota konstrukcji oraz łatwość w obsłudze. Dzięki zastosowaniu sprężonego powietrza jako medium roboczego, maszyny te są często lżejsze i bardziej kompaktowe niż ich elektryczne odpowiedniki. Ponadto, systemy pneumatyczne charakteryzują się dużą niezawodnością oraz długowiecznością, co sprawia, że są one idealnym rozwiązaniem dla przemysłu wymagającego ciągłej pracy. Warto również wspomnieć o ich elastyczności – maszyny pneumatyczne mogą być łatwo dostosowane do zmieniających się potrzeb produkcyjnych. Niemniej jednak istnieją także pewne wady związane z budową maszyn pneumatycznych. Jedną z nich jest konieczność regularnego serwisowania systemu sprężonego powietrza oraz monitorowania jego ciśnienia. Dodatkowo, sprężone powietrze może być kosztowne w produkcji i dostarczaniu, co wpływa na ogólne koszty eksploatacji systemu.
Jakie zastosowania mają maszyny pneumatyczne w przemyśle
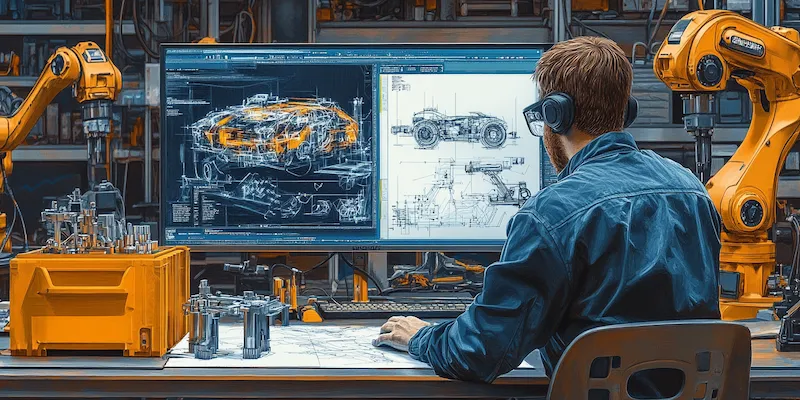
Maszyny pneumatyczne znajdują szerokie zastosowanie w różnych dziedzinach przemysłu ze względu na swoją wszechstronność oraz efektywność działania. W przemyśle motoryzacyjnym często wykorzystuje się je do montażu komponentów oraz do wykonywania operacji związanych z obróbką materiałów. Przykładem mogą być narzędzia pneumatyczne stosowane do przykręcania śrub czy też malowania powierzchni samochodów. W branży spożywczej maszyny pneumatyczne są wykorzystywane do pakowania produktów oraz transportu surowców. Dzięki swojej higienicznej konstrukcji oraz możliwości łatwego czyszczenia, idealnie nadają się do pracy w warunkach wymagających zachowania wysokich standardów sanitarnych. W przemyśle chemicznym i farmaceutycznym maszyny te służą do dozowania substancji oraz mieszania składników chemicznych. Co więcej, w automatyce przemysłowej maszyny pneumatyczne odgrywają kluczową rolę w systemach transportowych oraz robotyzacji procesów produkcyjnych.
Jakie nowoczesne technologie wspierają budowę maszyn pneumatycznych
W ostatnich latach rozwój technologii znacząco wpłynął na budowę maszyn pneumatycznych oraz ich efektywność działania. Jednym z najważniejszych trendów jest automatyzacja procesów produkcyjnych, która pozwala na zwiększenie wydajności oraz redukcję kosztów operacyjnych. Dzięki zastosowaniu nowoczesnych systemów sterowania oraz czujników, maszyny pneumatyczne mogą pracować z większą precyzją i niezawodnością. Kolejnym ważnym aspektem jest rozwój materiałów kompozytowych oraz lekkich stopów metali, które pozwalają na budowę bardziej wytrzymałych i jednocześnie lżejszych konstrukcji maszyn pneumatycznych. Warto również zwrócić uwagę na innowacje związane z technologią sprężania powietrza oraz odzyskiwania energii z procesów roboczych. Nowoczesne sprężarki wyposażone są w zaawansowane układy zarządzania energią, co pozwala na znaczne obniżenie kosztów eksploatacji systemu. Dodatkowo rozwój technologii Internetu Rzeczy (IoT) otwiera nowe możliwości monitorowania stanu maszyn oraz optymalizacji ich pracy na podstawie danych zbieranych w czasie rzeczywistym.
Jakie są kluczowe zasady bezpieczeństwa w pracy z maszynami pneumatycznymi
Bezpieczeństwo w pracy z maszynami pneumatycznymi jest niezwykle istotnym aspektem, który powinien być brany pod uwagę na każdym etapie użytkowania tych urządzeń. Przede wszystkim, przed rozpoczęciem pracy z maszyną pneumatyczną, należy dokładnie zapoznać się z instrukcją obsługi oraz zasadami BHP. Użytkownicy powinni być odpowiednio przeszkoleni w zakresie obsługi sprzętu oraz rozpoznawania potencjalnych zagrożeń. Ważne jest również, aby regularnie przeprowadzać przeglądy techniczne maszyn, co pozwala na wczesne wykrywanie ewentualnych usterek i zapobieganie awariom. Kolejnym kluczowym elementem jest stosowanie odpowiednich środków ochrony osobistej, takich jak rękawice, gogle czy zatyczki do uszu, które chronią pracowników przed szkodliwymi skutkami hałasu oraz ewentualnymi urazami mechanicznymi. Należy także zwrócić uwagę na właściwe oznakowanie strefy pracy oraz umiejscowienie urządzeń zabezpieczających, takich jak osłony czy wyłączniki awaryjne. Warto również unikać pracy w pobliżu źródeł wilgoci lub substancji łatwopalnych, które mogą stanowić dodatkowe zagrożenie.
Jakie są najczęstsze problemy związane z maszynami pneumatycznymi
Maszyny pneumatyczne, mimo swojej niezawodności, mogą napotykać różne problemy w trakcie użytkowania. Jednym z najczęstszych problemów jest niewłaściwe ciśnienie powietrza, które może prowadzić do nieefektywnej pracy siłowników oraz innych komponentów systemu. Zbyt niskie ciśnienie może powodować spadek wydajności maszyny, podczas gdy zbyt wysokie ciśnienie może prowadzić do uszkodzenia elementów konstrukcyjnych. Innym powszechnym problemem są wycieki sprężonego powietrza, które mogą występować w wyniku zużycia uszczelek lub niewłaściwego montażu przewodów. Takie wycieki nie tylko wpływają na efektywność działania maszyny, ale również zwiększają koszty eksploatacji poprzez marnotrawstwo energii. Dodatkowo, zanieczyszczenia w systemie powietrza mogą prowadzić do uszkodzenia narzędzi pneumatycznych oraz innych elementów maszyny. Dlatego tak ważne jest regularne czyszczenie filtrów oraz stosowanie osuszaczy powietrza. Wreszcie, problemy związane z elektroniką i systemami sterującymi mogą również wpłynąć na działanie maszyn pneumatycznych.
Jakie są przyszłe kierunki rozwoju technologii maszyn pneumatycznych
Przyszłość technologii maszyn pneumatycznych zapowiada się bardzo obiecująco, a wiele innowacji ma potencjał znacząco poprawić ich wydajność i funkcjonalność. Jednym z kluczowych kierunków rozwoju jest integracja systemów pneumatycznych z technologią cyfrową i automatyzacją procesów przemysłowych. Dzięki zastosowaniu sztucznej inteligencji oraz analizy danych w czasie rzeczywistym, możliwe będzie optymalizowanie pracy maszyn oraz szybsze diagnozowanie ewentualnych usterek. Ponadto rozwój technologii Internetu Rzeczy (IoT) umożliwi monitorowanie stanu maszyn na odległość oraz automatyczne dostosowywanie parametrów pracy do zmieniających się warunków produkcyjnych. Kolejnym interesującym kierunkiem jest poszukiwanie bardziej ekologicznych rozwiązań w zakresie sprężania powietrza oraz odzyskiwania energii. Inżynierowie pracują nad nowymi metodami sprężania powietrza, które będą bardziej energooszczędne i przyjazne dla środowiska. Warto również zwrócić uwagę na rozwój materiałów kompozytowych i lekkich stopów metali, które mogą znacząco wpłynąć na konstrukcję maszyn pneumatycznych, czyniąc je lżejszymi i bardziej wytrzymałymi.
Jakie są najważniejsze trendy w projektowaniu maszyn pneumatycznych
W projektowaniu maszyn pneumatycznych można zaobserwować kilka kluczowych trendów, które mają na celu zwiększenie ich efektywności oraz funkcjonalności. Pierwszym z nich jest miniaturyzacja komponentów, co pozwala na tworzenie bardziej kompaktowych i lekkich konstrukcji. Dzięki temu maszyny pneumatyczne mogą być łatwiej integrowane w istniejące linie produkcyjne oraz zajmować mniej miejsca w zakładach przemysłowych. Kolejnym ważnym trendem jest modularność projektowania, która umożliwia łatwe dostosowywanie maszyn do zmieniających się potrzeb produkcyjnych. Modułowe podejście pozwala na szybkie wymienianie lub dodawanie nowych komponentów bez konieczności całkowitej przebudowy systemu. Dodatkowo rośnie znaczenie ergonomii w projektowaniu maszyn pneumatycznych – inżynierowie starają się tworzyć urządzenia przyjazne dla użytkownika, które minimalizują ryzyko urazów i zmęczenia podczas pracy. Warto również zauważyć rosnącą popularność technologii symulacji komputerowej w procesie projektowania maszyn pneumatycznych.
Jakie są kluczowe różnice między maszynami elektrycznymi a pneumatycznymi
Maszyny elektryczne i pneumatyczne to dwa różne typy urządzeń wykorzystywanych w przemyśle, które mają swoje unikalne cechy oraz zastosowania. Główna różnica między nimi polega na medium roboczym – maszyny elektryczne wykorzystują energię elektryczną do napędu silników i mechanizmów roboczych, podczas gdy maszyny pneumatyczne korzystają ze sprężonego powietrza jako źródła energii. To sprawia, że maszyny pneumatyczne często charakteryzują się większą prostotą konstrukcji oraz mniejszą wagą niż ich elektryczne odpowiedniki. Z drugiej strony maszyny elektryczne zazwyczaj oferują wyższą precyzję działania oraz lepszą kontrolę nad parametrami pracy. W przypadku zastosowań wymagających dużej dokładności lub skomplikowanych ruchów mechanicznych lepszym wyborem mogą być maszyny elektryczne. Kolejną istotną różnicą jest koszt eksploatacji – sprężone powietrze może być droższe niż energia elektryczna, co wpływa na ogólne koszty użytkowania systemu pneumatycznego. Jednakże maszyny pneumatyczne często wymagają mniejszej konserwacji i są mniej podatne na awarie związane z przegrzewaniem się silników elektrycznych.