Budowa maszyn produkcyjnych to złożony proces, który wymaga uwzględnienia wielu kluczowych elementów. W pierwszej kolejności należy zwrócić uwagę na konstrukcję mechaniczną, która stanowi fundament każdej maszyny. To właśnie ona odpowiada za stabilność i wytrzymałość urządzenia, co jest niezwykle istotne w kontekście intensywnego użytkowania w warunkach przemysłowych. Kolejnym ważnym aspektem jest układ napędowy, który zapewnia odpowiednią moc oraz prędkość pracy maszyny. W zależności od zastosowania, może to być napęd elektryczny, hydrauliczny lub pneumatyczny. Dodatkowo, nie można zapominać o systemach sterowania, które umożliwiają precyzyjne zarządzanie pracą maszyny. Nowoczesne maszyny produkcyjne często wyposażone są w zaawansowane technologie automatyzacji oraz monitorowania, co pozwala na zwiększenie efektywności i bezpieczeństwa pracy.
Jakie materiały są najczęściej wykorzystywane w budowie maszyn
W procesie budowy maszyn produkcyjnych kluczową rolę odgrywają materiały, które muszą spełniać określone normy jakościowe oraz wytrzymałościowe. Najczęściej stosowanym materiałem jest stal, która charakteryzuje się wysoką odpornością na obciążenia mechaniczne oraz korozję. W przypadku maszyn narażonych na działanie wysokich temperatur lub agresywnych substancji chemicznych, wykorzystuje się stopy metali odpornych na te czynniki. Ponadto, coraz częściej w budowie maszyn wykorzystywane są tworzywa sztuczne, które dzięki swoim właściwościom mogą znacząco obniżyć wagę urządzenia i poprawić jego efektywność energetyczną. Warto również wspomnieć o zastosowaniu kompozytów, które łączą zalety różnych materiałów i znajdują zastosowanie w nowoczesnych rozwiązaniach inżynieryjnych.
Jakie technologie są wykorzystywane w budowie maszyn produkcyjnych
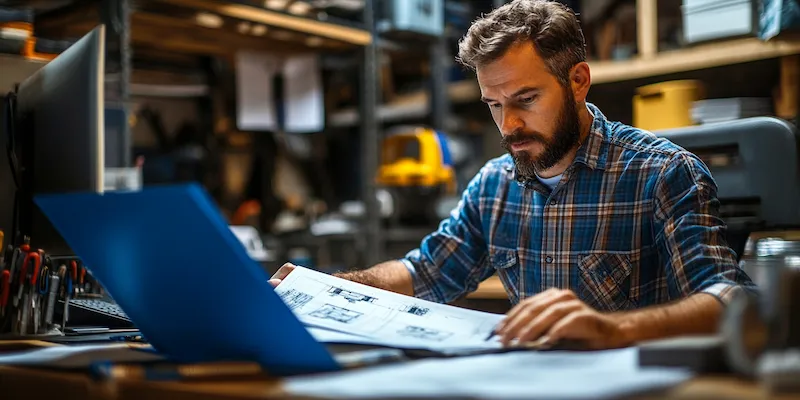
W budowie maszyn produkcyjnych coraz większą rolę odgrywają nowoczesne technologie, które pozwalają na zwiększenie wydajności oraz precyzji procesów produkcyjnych. Jednym z najważniejszych trendów jest automatyzacja, która obejmuje zarówno robotyzację linii produkcyjnych, jak i wdrażanie systemów sterowania opartych na sztucznej inteligencji. Dzięki temu możliwe jest osiągnięcie znacznie wyższej efektywności pracy oraz redukcja błędów ludzkich. Kolejnym istotnym aspektem jest wykorzystanie technologii druku 3D do prototypowania i produkcji części zamiennych. Ta innowacyjna metoda pozwala na szybkie wytwarzanie skomplikowanych kształtów przy minimalnym zużyciu materiału. Również cyfryzacja procesu projektowania maszyn poprzez modelowanie 3D oraz symulacje komputerowe umożliwia lepsze planowanie i optymalizację procesów produkcyjnych.
Jakie są najważniejsze etapy projektowania maszyn produkcyjnych
Projektowanie maszyn produkcyjnych to skomplikowany proces, który składa się z kilku kluczowych etapów. Pierwszym krokiem jest analiza potrzeb klienta oraz specyfikacji technicznych, które określają wymagania dotyczące funkcjonalności maszyny. Na tym etapie inżynierowie zbierają informacje o oczekiwaniach użytkowników oraz warunkach pracy urządzenia. Następnie przystępuje się do fazy koncepcyjnej, gdzie tworzone są wstępne projekty oraz modele 3D maszyny. Po zatwierdzeniu koncepcji następuje szczegółowe projektowanie poszczególnych komponentów oraz układów mechanicznych i elektronicznych. Ważnym etapem jest także testowanie prototypu, które pozwala na identyfikację ewentualnych problemów przed rozpoczęciem seryjnej produkcji.
Jakie są najczęstsze problemy w budowie maszyn produkcyjnych
Budowa maszyn produkcyjnych wiąże się z wieloma wyzwaniami, które mogą wpływać na jakość i efektywność finalnego produktu. Jednym z najczęstszych problemów jest niewłaściwy dobór materiałów, co może prowadzić do osłabienia konstrukcji oraz zwiększenia ryzyka awarii. W przypadku zastosowania materiałów o niskiej jakości, maszyna może nie spełniać oczekiwań użytkowników, co w konsekwencji prowadzi do wysokich kosztów napraw oraz przestojów w produkcji. Kolejnym istotnym problemem jest błędne zaprojektowanie układów mechanicznych, które mogą powodować nadmierne zużycie części lub ich uszkodzenia. Niekiedy zdarza się również, że maszyny nie są dostosowane do specyficznych warunków pracy, co może skutkować ich niewłaściwym działaniem. Warto także zwrócić uwagę na kwestie związane z ergonomią i bezpieczeństwem pracy, które często są pomijane na etapie projektowania.
Jakie są przyszłościowe kierunki rozwoju maszyn produkcyjnych
Przyszłość budowy maszyn produkcyjnych zapowiada się niezwykle interesująco, z uwagi na dynamiczny rozwój technologii oraz rosnące wymagania rynku. Jednym z kluczowych kierunków rozwoju jest dalsza automatyzacja procesów produkcyjnych, która pozwala na zwiększenie wydajności oraz redukcję kosztów operacyjnych. W miarę postępu technologicznego, coraz więcej przedsiębiorstw decyduje się na wdrażanie robotów przemysłowych, które potrafią wykonywać skomplikowane zadania z dużą precyzją i szybkością. Również sztuczna inteligencja odgrywa coraz większą rolę w optymalizacji procesów produkcyjnych, umożliwiając przewidywanie awarii oraz automatyczne dostosowywanie parametrów pracy maszyn. Kolejnym istotnym trendem jest rozwój technologii IoT, która pozwala na zbieranie danych o pracy maszyn w czasie rzeczywistym oraz ich analizę. Dzięki temu możliwe jest lepsze zarządzanie procesami produkcyjnymi oraz szybsze podejmowanie decyzji.
Jakie są kluczowe normy i standardy w budowie maszyn
Budowa maszyn produkcyjnych wymaga przestrzegania szeregu norm i standardów, które mają na celu zapewnienie bezpieczeństwa oraz jakości produktów. W Europie jednym z najważniejszych dokumentów regulujących te kwestie jest dyrektywa maszynowa 2006/42/WE, która określa wymagania dotyczące projektowania i budowy maszyn. Zgodność z tą dyrektywą jest niezbędna dla uzyskania oznakowania CE, co pozwala na wprowadzenie maszyny na rynek europejski. Ponadto, istnieją różne normy ISO dotyczące jakości i bezpieczeństwa, takie jak ISO 9001 czy ISO 12100, które stanowią podstawę dla systemów zarządzania jakością w przedsiębiorstwach zajmujących się budową maszyn. Kluczowe znaczenie ma również przestrzeganie norm dotyczących ochrony środowiska oraz efektywności energetycznej, co staje się coraz bardziej istotne w kontekście globalnych działań na rzecz zrównoważonego rozwoju.
Jakie umiejętności są potrzebne do projektowania maszyn produkcyjnych
Aby skutecznie projektować maszyny produkcyjne, inżynierowie muszą posiadać szereg umiejętności technicznych oraz interpersonalnych. Kluczową kompetencją jest znajomość zasad mechaniki oraz inżynierii materiałowej, co pozwala na właściwe dobieranie komponentów oraz tworzenie stabilnych konstrukcji. Umiejętności związane z modelowaniem 3D oraz symulacjami komputerowymi są również niezbędne do opracowywania efektywnych projektów maszyn. Współczesny inżynier powinien być także zaznajomiony z nowoczesnymi technologiami automatyzacji oraz programowaniem systemów sterowania, co umożliwia tworzenie inteligentnych rozwiązań produkcyjnych. Oprócz umiejętności technicznych ważne są także kompetencje miękkie, takie jak umiejętność pracy zespołowej oraz komunikacji z innymi działami firmy. Projektowanie maszyn często wymaga współpracy z innymi specjalistami, takimi jak technolodzy czy specjaliści ds. jakości.
Jakie są koszty budowy maszyn produkcyjnych
Koszty budowy maszyn produkcyjnych mogą znacząco różnić się w zależności od wielu czynników, takich jak skomplikowanie projektu, zastosowane materiały czy technologie. Na początku procesu projektowania warto przeprowadzić dokładną analizę kosztów związanych z poszczególnymi etapami budowy maszyny. Koszty materiałów stanowią często największy udział w całkowitych wydatkach, dlatego ich odpowiedni dobór ma kluczowe znaczenie dla rentowności projektu. Dodatkowo należy uwzględnić koszty robocizny związane z zatrudnieniem specjalistów odpowiedzialnych za projektowanie i montaż maszyny. Nie można zapominać o wydatkach związanych z testowaniem prototypu oraz certyfikacją zgodności z obowiązującymi normami i standardami. Koszty eksploatacyjne również mają znaczenie – obejmują one konserwację maszyny oraz ewentualne naprawy po jej uruchomieniu.
Jakie są zalety inwestycji w nowoczesne maszyny produkcyjne
Inwestycja w nowoczesne maszyny produkcyjne przynosi wiele korzyści dla przedsiębiorstw działających w różnych branżach przemysłowych. Przede wszystkim nowoczesne maszyny charakteryzują się wyższą wydajnością i precyzją działania niż starsze modele, co przekłada się na zwiększenie efektywności procesów produkcyjnych. Dzięki automatyzacji możliwe jest ograniczenie błędów ludzkich oraz zwiększenie tempa produkcji bez konieczności zatrudniania dodatkowych pracowników. Nowe technologie często wiążą się także z mniejszym zużyciem energii i surowców, co przyczynia się do obniżenia kosztów operacyjnych i pozytywnie wpływa na środowisko naturalne. Inwestycja w nowoczesne maszyny to również krok ku innowacjom – przedsiębiorstwa mogą szybciej reagować na zmieniające się potrzeby rynku oraz dostosowywać swoje produkty do oczekiwań klientów.
Jakie są wyzwania związane z serwisowaniem maszyn produkcyjnych
Serwisowanie maszyn produkcyjnych to kluczowy element zapewniający ich długotrwałe i niezawodne działanie. Wyzwania związane z tym procesem mogą być różnorodne i wymagają odpowiedniego podejścia ze strony przedsiębiorstw. Przede wszystkim, jednym z głównych problemów jest dostępność części zamiennych, które mogą być trudne do zdobycia, zwłaszcza w przypadku starszych modeli maszyn. Dodatkowo, czas przestoju maszyny podczas naprawy może prowadzić do znacznych strat finansowych, dlatego ważne jest, aby serwis był przeprowadzany szybko i efektywnie. Kolejnym wyzwaniem jest konieczność posiadania wykwalifikowanego personelu, który potrafi diagnozować problemy oraz przeprowadzać naprawy zgodnie z obowiązującymi normami i standardami. Warto również zwrócić uwagę na regularne przeglądy techniczne, które pozwalają na wczesne wykrywanie usterek i zapobiegają poważniejszym awariom.